Manufacturing
Our overseas manufacturing facilities enable localized production, offering customers enhanced flexibility, reduced lead times, and a stronger supply chain.
- Home
- Manufacturing
Robust Manufacturing Capabilities and Facilities
Our manufacturing capabilities and production infrastructure enable us to build multiple international research and production centers across the world which together form a comprehensive industry chain system. Our advanced production lines cover all aspects from cell manufacturing to system integration, ensuring top industry standards through strict process control and quality management.
6 Production Bases
6 Production Bases
Covering Wenzhou, Jiashan, Liuzhou, Foshan, Chongqing, and Indonesia.
90+GWh Capacity
90+GWh Capacity
By 2025, REPT BATTERO is expected to reach 90+ GWh of capacity to meet global demand for power and energy storage batteries.
580,000㎡ Single Mega Factory
580,000㎡ Single Mega Factory
Supporting large-scale battery production and development.
Committed to Creating Green and Smart Factories
Our continuous innovation in smart factory development helps us solve problems that include low R&D efficiency and high manual labor and production quality fluctuations. AI integration has enabled us to build zero-carbon factories which optimize production and enhance operational efficiency. Our smart manufacturing model operates at multiple bases to promote sustainable green development while leading the energy transformation.
Core Strength of Our Factory
Extreme Manufacturing
- Single-line production capacity >10GWh annually.
- 50PPM automated production lines for maximum efficiency with square aluminum shell production.
- Lean quality control with >6000 control points and >1000 AI monitoring systems ensuring precision.
Sustainable Manufacturing
- Next-gen zero-carbon factory with smart energy management and solar power applications.
- AI-driven digital twins and advanced manufacturing models to enhance efficiency.
- 30GWh super factory increases space utilization >30%, boosting capacity.
Ongoing Smart Factory Transformation and Upgrades
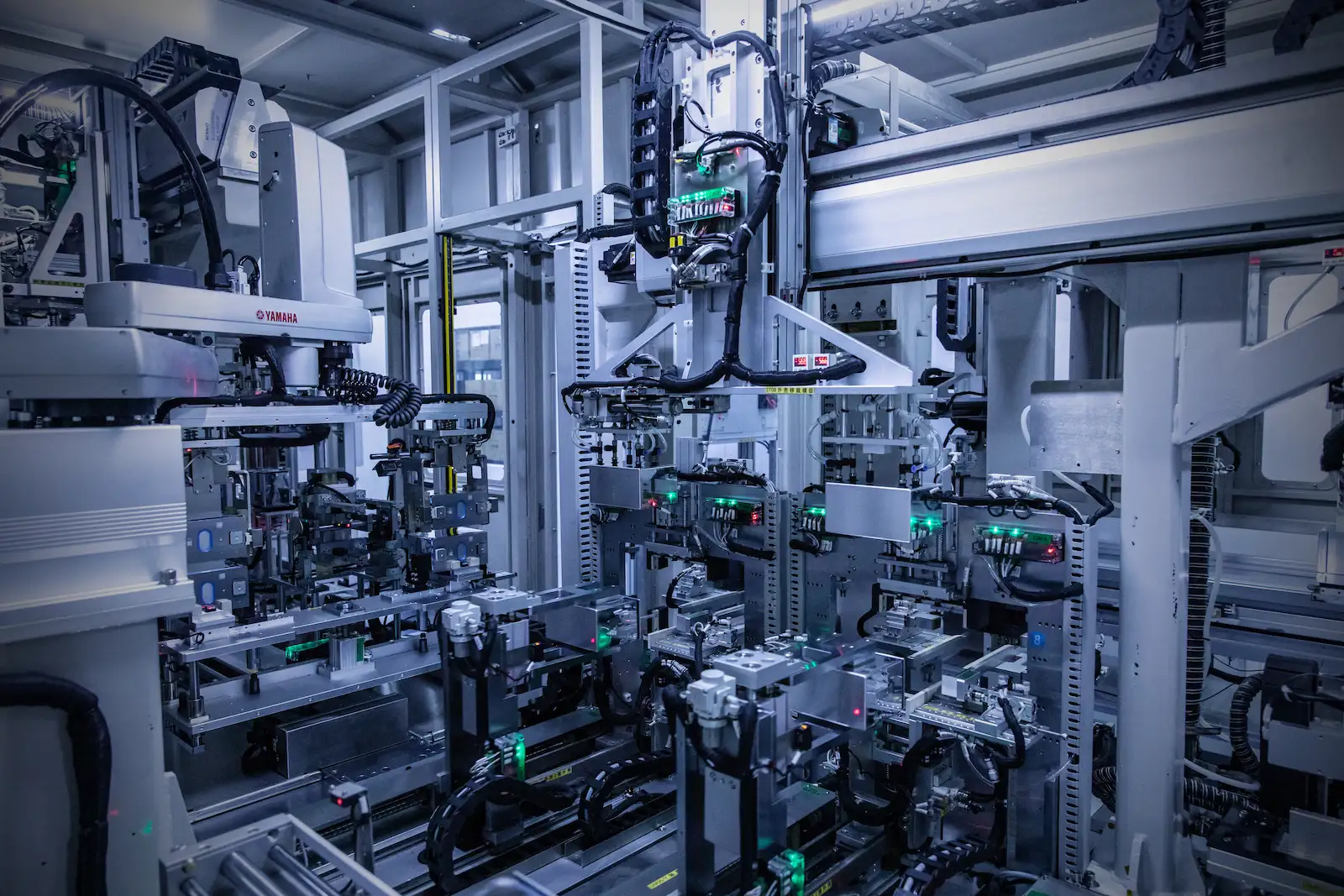
Smart Production Lines
- Automatic Data Upload: 90% of production data uploads automatically in real-time for smart monitoring and optimization.
- High-Precision CNC: >90% of key equipment is CNC automated, ensuring precision and efficiency.
- Wending Battery Smart Production Line: 2 Wending smart production lines to produce 314Ah batteries and set industry standards.
- Flexible Large-Scale Production: Production lines designed for 20PPM, offering flexibility and upgrade compatibility.
- Optimized Equipment Layout: High-precision automation equipment optimized for same-width models, improving efficiency.
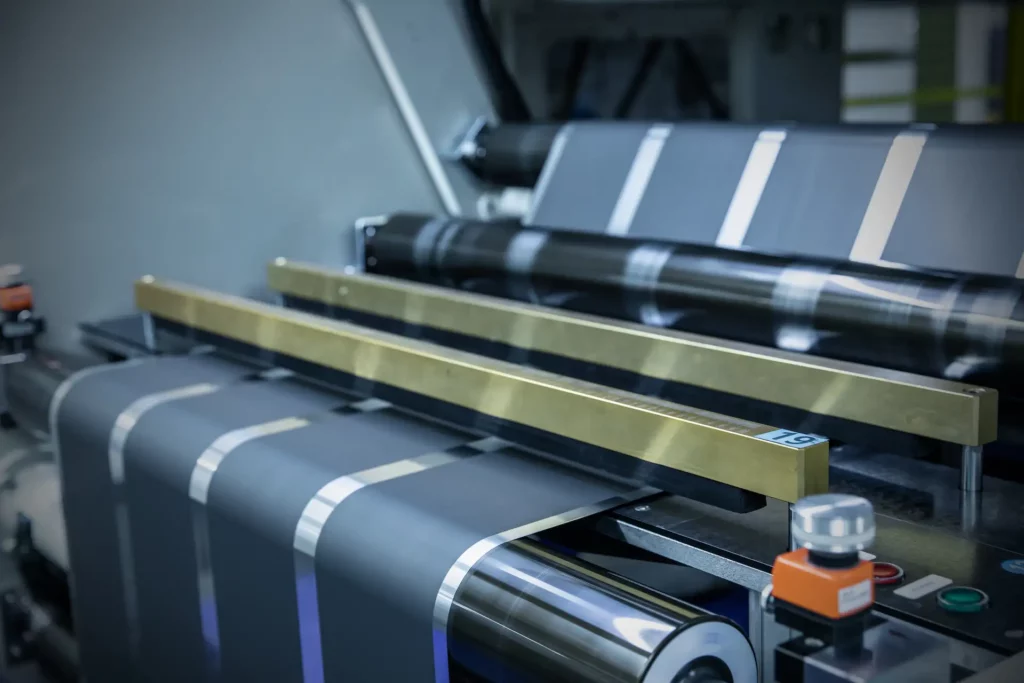
Fully Automated Production
- Visual Management: Human-machine interface for smart equipment control and production process visualization.
- Tab Laser Welding: Integrated laser welding technology optimizes battery space and avoids traditional welding issues.
- Intelligent Equipment Management: Real-time monitoring via connected devices and MES systems to optimize efficiency and maintenance.
- Automated Inspection and Monitoring: AI vision CCD and online systems monitor product quality, ensuring NG rate below 1%.
- Automated Handling System: AGVs, automated loading/unloading robots, and logistics lines optimize material handling and FIFO management.
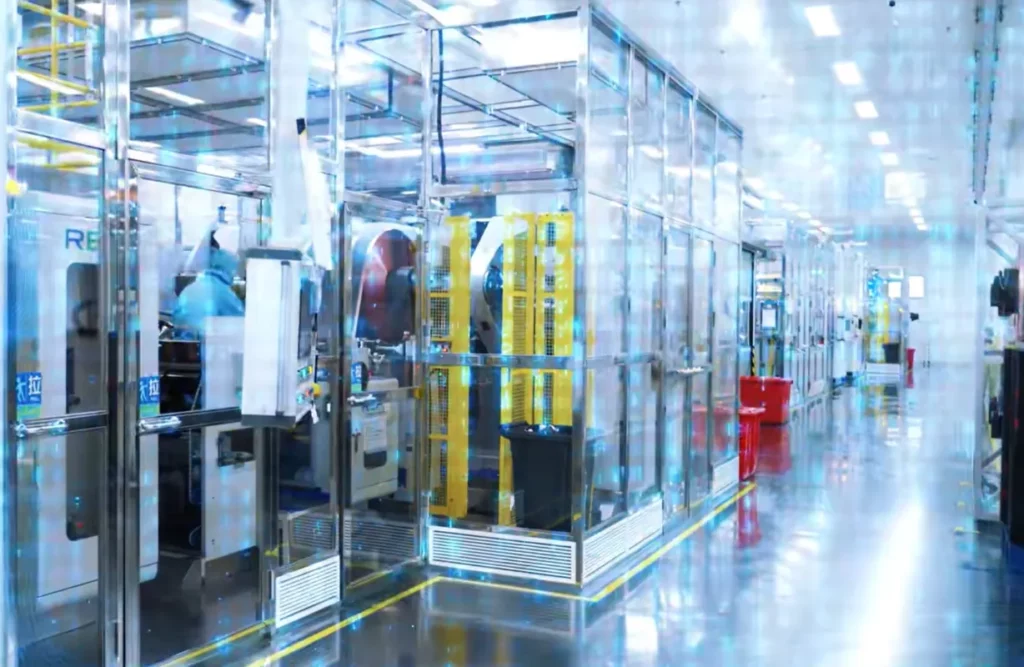
Information Management System
- System Integration and Digital Management: Fully digitalizes the production process with MES, PLM, ERP, WMS, SRM, and OA systems to enhance efficiency and collaboration.
- Intelligent Automation Monitoring: Integrates PLC, Andon, AGV, and self-control systems for smart management, anomaly detection, and automated material handling.
- End-to-End Digital Control: Ensures efficient execution and traceability from design to production through precise digital management.
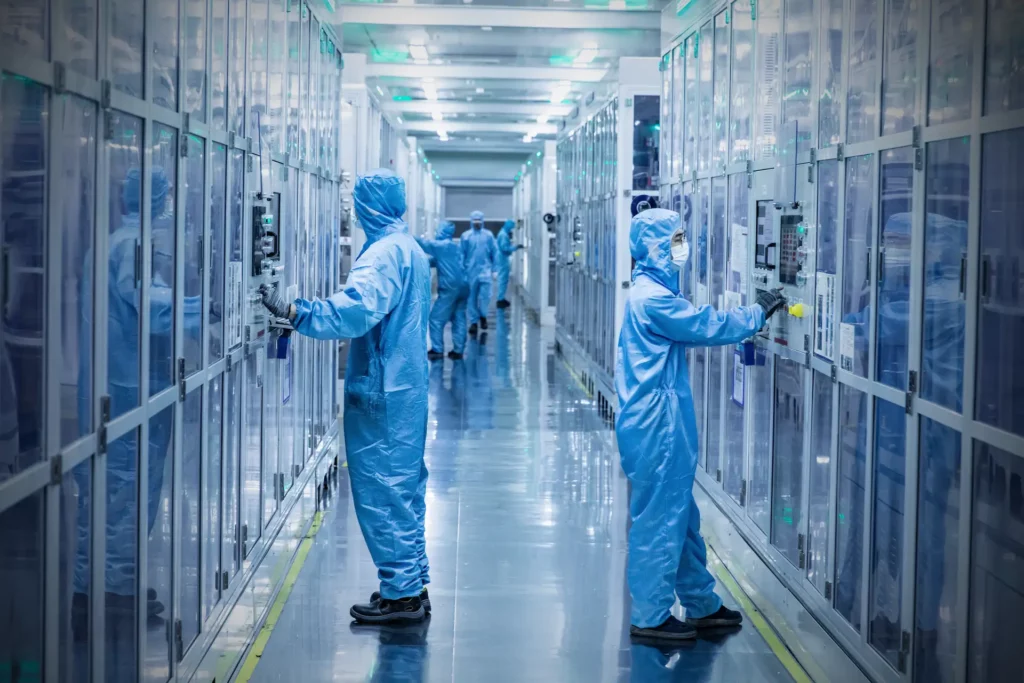
Environmental Management
- Temperature and Humidity Control: Real-time monitoring and adjustment of temperature and humidity on the production line to maintain a stable environment.
- Clean Environment: Class 10000 cleanroom management ensures a high-standard clean environment, preventing contamination. management ensures a high-standard clean environment, preventing contamination.
- Dust Control: Dust and particle levels are minimized through a cleanroom system, preserving product cleanliness and quality.
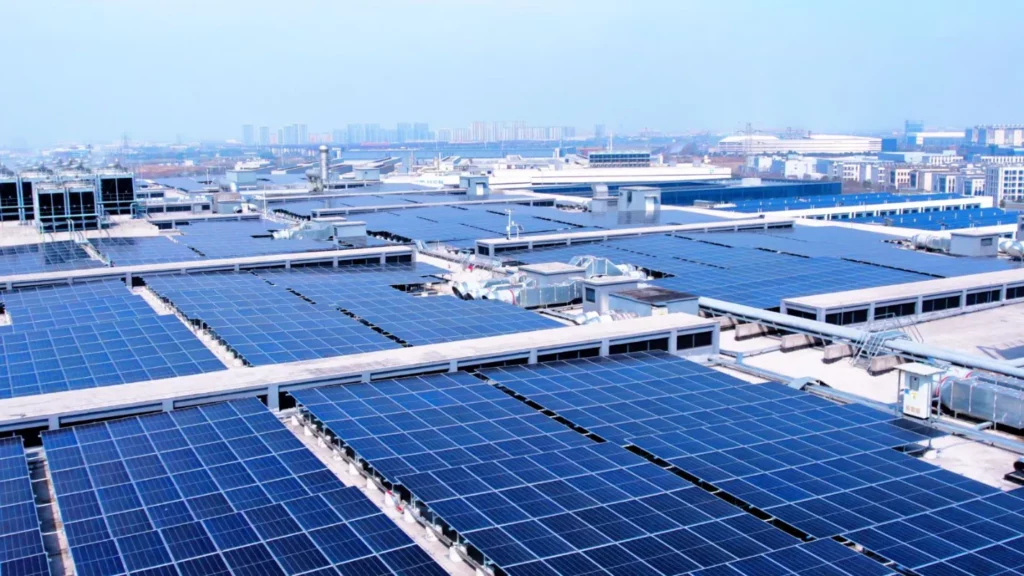
Energy Management
- Green Power: Solar systems on the factory roof supply part of the energy for production, supporting sustainability and lowering energy costs and carbon emissions.
- Environmental and Water Treatment Monitoring: Real-time monitoring of key facilities like pure water, wastewater, and vacuum pumps through self-control and MES systems, optimizing environmental and energy management.
Take a Look at Our Battery Cell Production Process
Trust in Our Production Quality
We are dedicated to delivering comprehensive quality, safety, and reliability assurance to our customers. By integrating standards development, product certification, functionality, performance, safety, and reliability testing with predictive analysis, we provide the most reliable product solutions.